Inventory control issues usually stem from too much or too little stock, impacting costs and efficiency.
Kanban is an ideal solution to these issues, as it restocks items only when required. Its visual framework and pull-based model keep stock flowing according to actual demand.
In this guide, I'll explain how to use Kanban in an inventory system to reduce excess and better control stock levels.
In this article
What Is Kanban?
Kanban began at Toyota in the 1940s, designed by engineer Taiichi Ohno. He noticed how supermarkets restocked only as shelves emptied. Then, he applied this pull-based idea to production, ensuring manufacturing only met actual demand.
This approach reduced waste and became fundamental to Toyota’s operations. Kanban principles now apply broadly to inventory and project management.
Core Principles
Kanban revolves around six guiding principles:
- Visualize Workflow: Make work visible to easily spot issues and tune up.
- Limit Work in Progress: Finish tasks before starting new ones to provide a steady flow.
- Manage Flow: Track the movement of work to discover areas to enhance.
- Clarify Process Policies: Share workflow rules so everyone is aligned.
- Use Feedback Loops: Encourage feedback to find ways to improve quickly.
- Improve Through Collaboration: Continuously learn and experiment as a team.
Key Elements
The essential elements of Kanban are:
- Kanban Board: It shows tasks in columns like To Do, In Progress, and Done.
- Kanban Cards: They represent tasks that shift through stages as progress is made.
- WIP Limits: These ensure that each stage is manageable, improving workflow efficiency.
Benefits
- Kanban makes progress visible to everyone, improving team coordination and collaboration.
- It recedes waste by controlling inventory, leading to cost and space savings.
- Kanban simplifies how teams stay flexible, shifting priorities as needed without losing efficiency.
- Also, it speeds up work processes by showing where bottlenecks occur, helping teams fix them faster.
How to Use Kanban in Inventory Management?
What is Kanban inventory management?
Kanban inventory management visually monitors stock levels to reduce waste and avoid excess. It relies on signals to prompt reordering according to demand. This method helps businesses manage stock stages and limits ongoing work.
How to Apply Kanban in Inventory Management?
Apply Kanban to your inventory management with this guide, focusing on system analysis and ongoing improvements.
Step 1 Evaluate Your Current Inventory Process
Analyze your existing inventory approach to find gaps and make room for a more efficient Kanban system.
- Spot Bottlenecks: Look for steps that cause delays, like lengthy ordering times. Identify areas where materials stack up and clog the workflow.
- Control Waste: Check if your inventory has too much or too little stock. Overstock takes up space and locks up funds, while understock disrupts production and upsets customers. Pay attention to items that might expire or aren’t selling.
- Identify Improvement Opportunities: Evaluate if your process can handle sudden demand increases. For instance, could you ramp up stock if a product's demand spiked? Identify what's manual, as Kanban may help you automate it.
Step 2 Design Your Kanban System
With a clear picture of your system's current shortcomings, craft a personalized Kanban model.
- Define Workflow Stages: Outline each stage in your inventory process, such as Order Materials, Receive Stock, and Ready for Use. These stages should align with your workflow for effective monitoring.
- Set Up Kanban Cards: Represent each inventory item with a Kanban card. Include key details like name, quantity, reorder point, and supplier. For instance, for perishable goods, include an expiration date field. Customize cards to fit the type of item, such as adding reorder levels for bakery ingredients.
- Establish WIP Limits: Set work-in-progress limits based on your demand and available storage space. For example, cap Order Materials to prevent over-ordering.
Step 3 Implement Your Kanban System
With your Kanban board in place, the focus now shifts to bringing your team on board and finalizing the system setup.
- Train Your Team: Teach them how it will streamline inventory tasks to update the board and manage Kanban cards. Assign roles for keeping inventory status accurate.
- Set Up the Board: Choose a digital or physical board that suits your needs. Arrange it by workflow stages. Place each item’s card at the right stage; for example, move flour to Order Materials when it needs reordering.
- Daily Use of Kanban Cards: Integrate Kanban cards into your daily routine. Move a card to the Order Materials stage when stock needs to be ordered, then update it as items arrive. This real-time tracking helps avoid shortages and overstock.
Step 4 Monitor and Improve Your System
Check your system’s performance regularly after launch. Small tweaks can enhance efficiency.
Track Key Metrics
- Lead time is a key measure of restocking speed. The quicker it is, the sooner you can fulfill demand.
- Then, check Cycle Time, such as how long items stay in the process. Longer times may reveal bottlenecks.
- Finally, track Inventory Turnover. High turnover is efficient; low turnover might mean overstock.
Refine as Needed
- Use these metrics to spot issues. If Order Materials delays restocking, adjust reorder points.
- For piled-up items, decrease WIP limits to smooth flow. Minor tweaks, like updating Kanban cards, can enhance the system.
- Include team feedback—they know where improvements are needed.
Practical Tips for Kanban Inventory Management
- Optimize card design. Ensure each card includes the necessary details. This makes tracking simple and helps with reordering.
- Pick the right board format. Consider a digital board for real-time updates if you manage inventory across multiple locations.
- Use color coding for clarity. Color-code cards by type, urgency, or supplier on physical boards for quick recognition.
- Conduct regular reviews. Monthly or quarterly checks ensure your Kanban system stays effective and responsive to demand.
Create Your Kanban on a Simple Tool
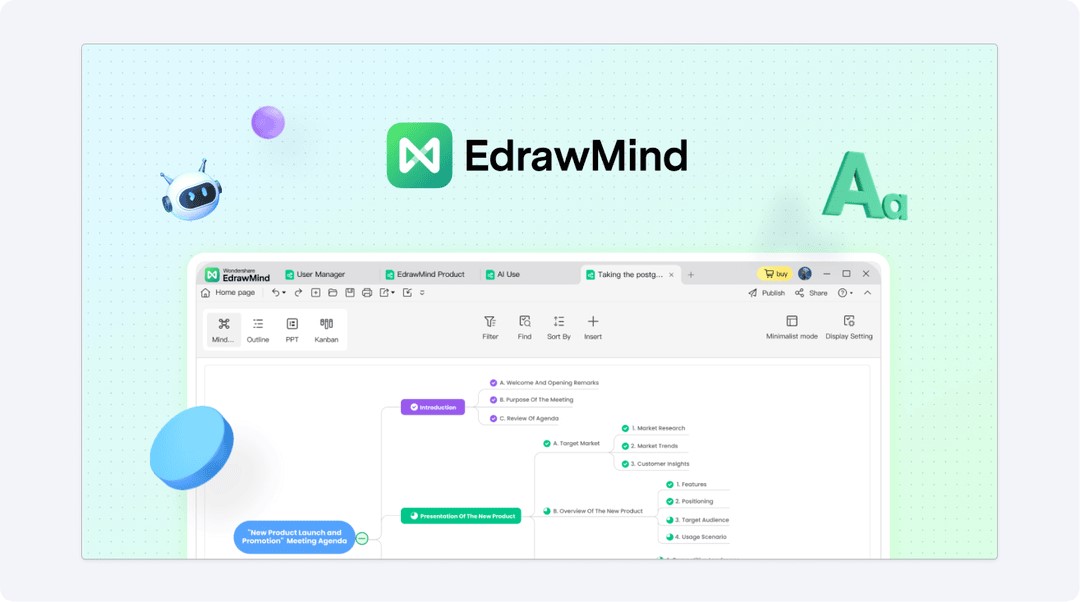
Task management can be tedious and full of errors if you use spreadsheets or paper. As your business expands, you need something more effective. EdrawMind offers a more visual and flexible solution to meet those needs.
It combines mind mapping and task management features, including a Kanban tool for easy workflow and inventory tracking. Though part of the paid plan, its user-friendly interface simplifies organization.
Here’s how to set up your Kanban using EdrawMind:

Step 1 Create a New Project
Open EdrawMind Desktop and click the Create button.
Select the Task Kanban option to set up a basic Kanban framework.
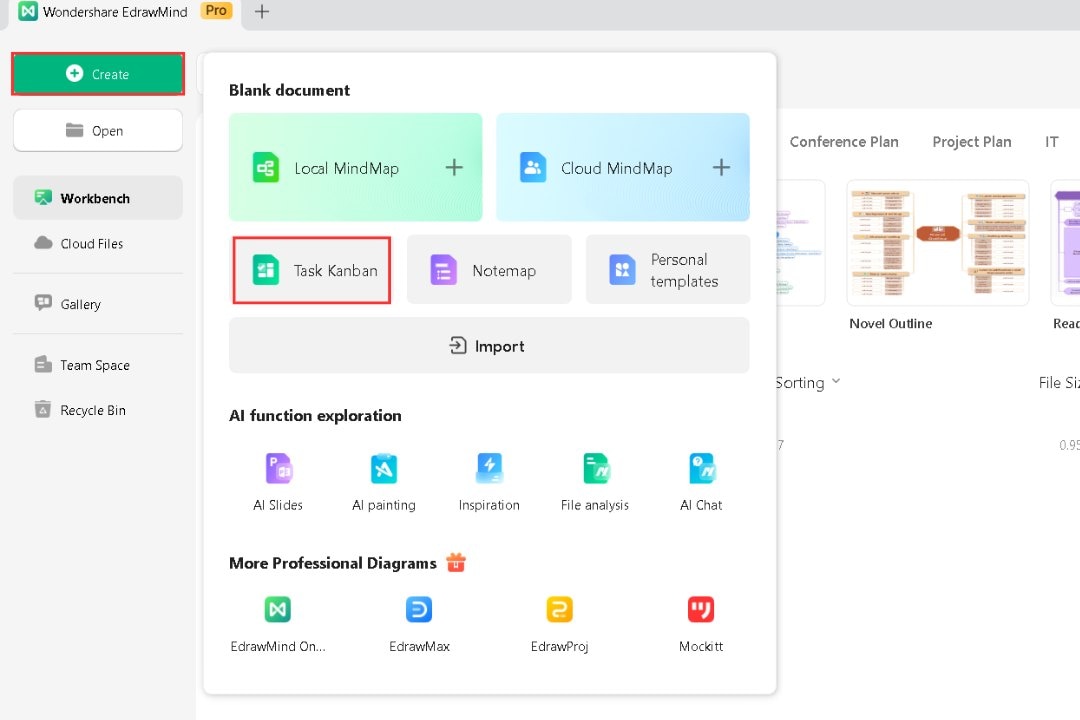
Step 2 Set Up Your Workflow Stages
Set up your task stages. EdrawMind gives you To-Do, In Progress, and Done by default. Click to change a column’s name based on your workflow. For inventory, you can use:
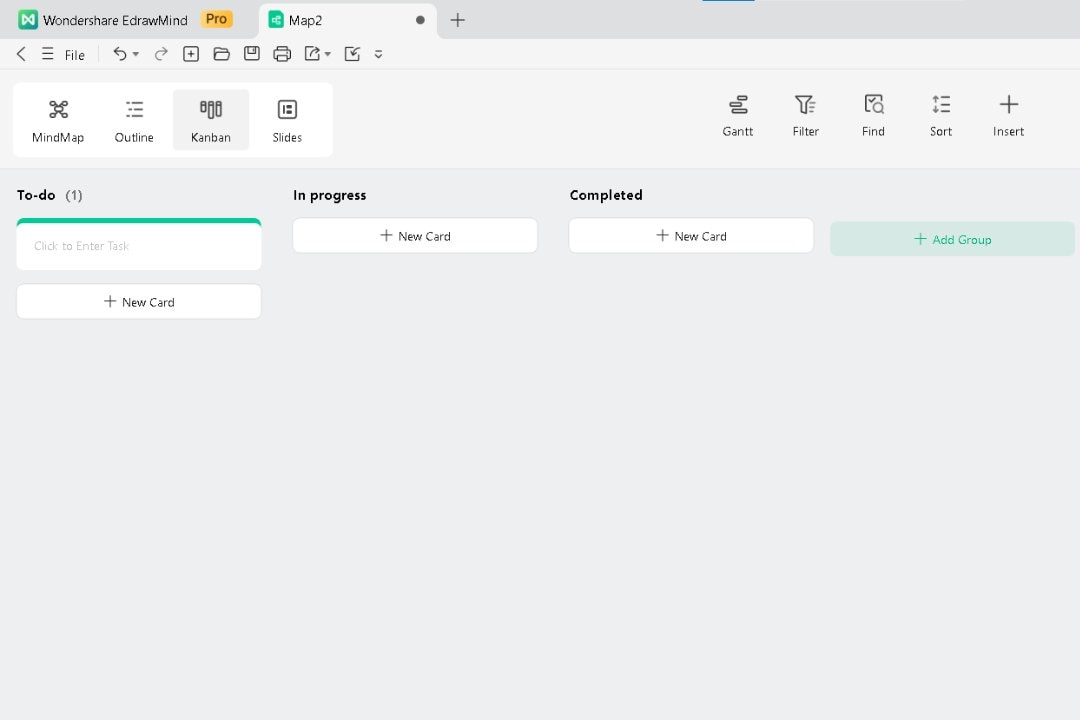
Step 3 Add Tasks to Your Kanban Board
Once your stages are in place, start adding tasks.
Click New Card in the To-Do column or edit the old one. This will help you track inventory tasks. Example: To add minor details in bullets, click the card and hit enter.
Select a card and customize its color based on your preference from the right-side menu.
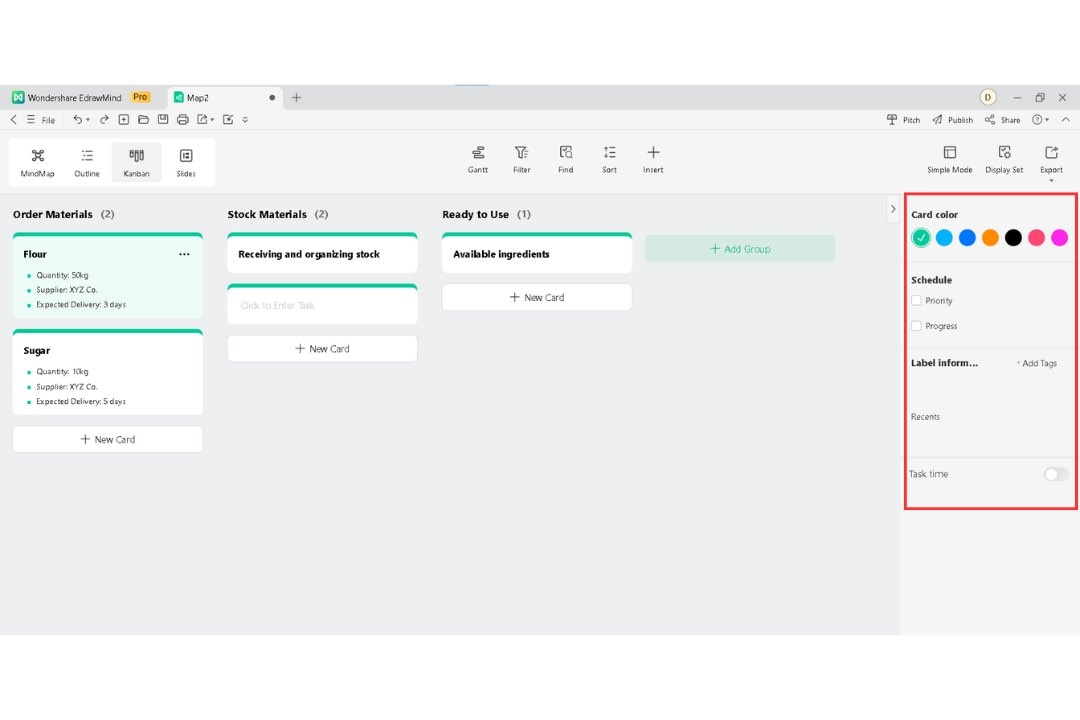
Step 4 Update Task Status
As tasks progress, update their status on the board. Simply drag and drop them across the columns.
Once you’ve ordered the flour in the Order Materials stage, move the task to Stock Materials. When the flour is ready to use, drag the task to Ready to Use.
This method helps you see where each task stands.
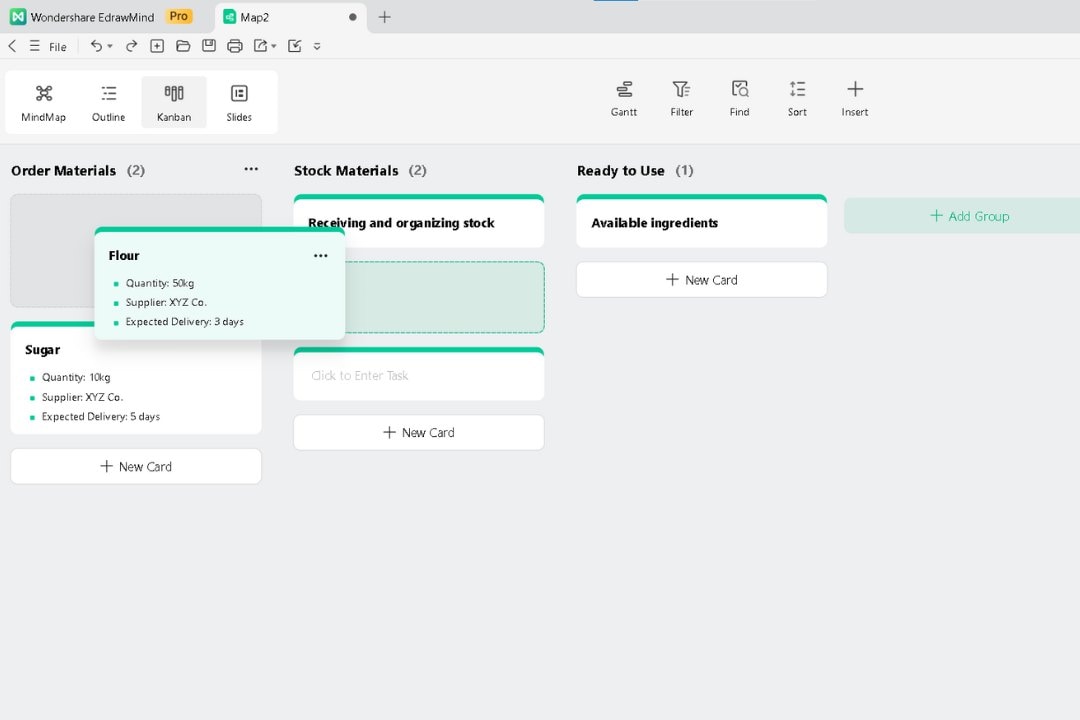
Step 5 Exporting Your Kanban
Click the Export button and select the More format option. Choose the required format from the multiple available options. Adjust settings (e.g., page size, resolution).
Click Export and your file will be downloaded to your computer.
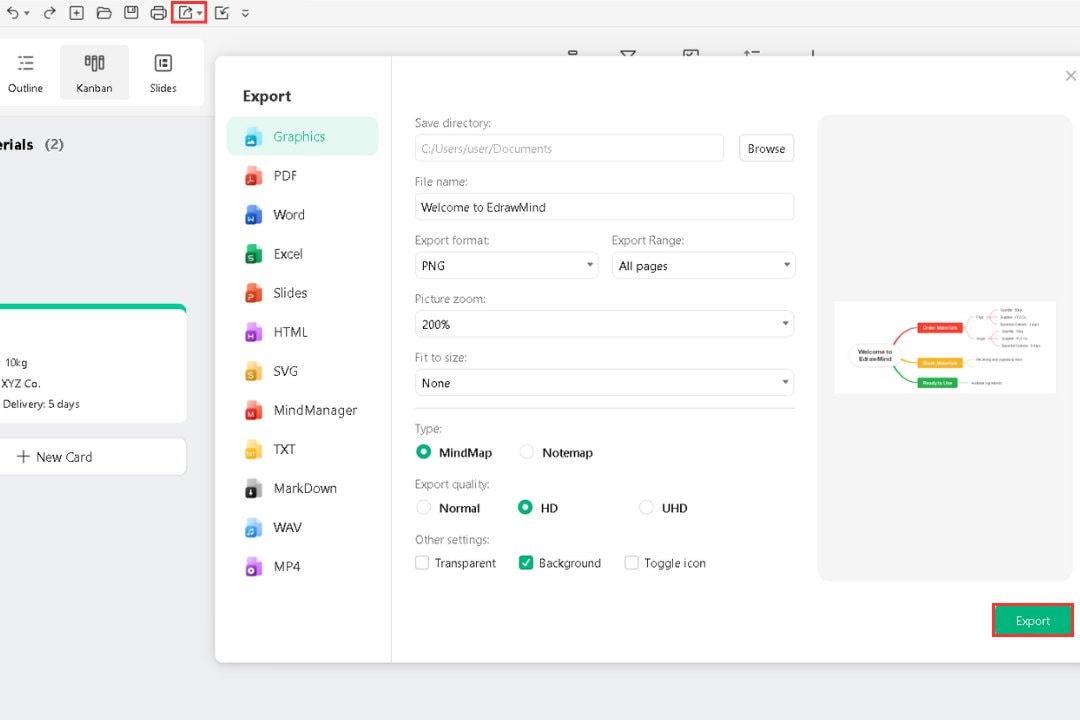
Conclusion
In a nutshell, Kanban simplifies inventory management. Visualizing workflows and limiting tasks helps businesses keep operations efficient and reduce waste.
To handle a bakery’s inventory issues, I’ve seen how well it works for large and small businesses.
While physical boards work well, EdrawMind offers a more flexible, digital approach. It helps you customize your workflows and track inventory quickly. So, try it today and create your kanban easily.
