Kanban is a visual workflow management tool designed to optimize processes and improve efficiency. Originating from Toyota’s manufacturing system, it has evolved into a versatile methodology for project management across industries. By visually tracking tasks, teams can identify bottlenecks and maintain smooth workflows.
This comprehensive guide explores the core principles of Kanban, including its benefits, key components, and real-world applications. Whether you're new to Kanban or looking to refine your processes, this resource provides practical insights for implementation.
Discover how Kanban fosters collaboration, enhances productivity, and ensures continuous improvement. From basic concepts to advanced strategies, this guide equips you with everything you need to master Kanban and streamline your projects effectively.
In this article
Part 1: What is Kanban
Kanban visualizes work processes and improves workflow efficiency. At its core, Kanban focuses on how tasks move through various stages, making managing and optimizing work easier.
A traditional Kanban board includes columns with labels such as 'To Do,' 'In Progress,' and 'Done,' representing steps in a process. Tasks are depicted as cards that move across these columns, providing a clear visual of the workflow. This approach helps teams identify bottlenecks and streamline operations.
Benefits of a Kanban
The primary goal of Kanban is to optimize processes and minimize inefficiencies. A key principle is managing "Work in Progress" (WIP), which limits the number of tasks handled simultaneously. This prevents overload, reduces lead times, and enhances scheduling.
Kanban emphasizes continuous improvement, encouraging teams to refine processes over time. Widely applicable in software, manufacturing, and other fields, Kanban is a flexible, customizable system aimed at boosting organization and productivity.
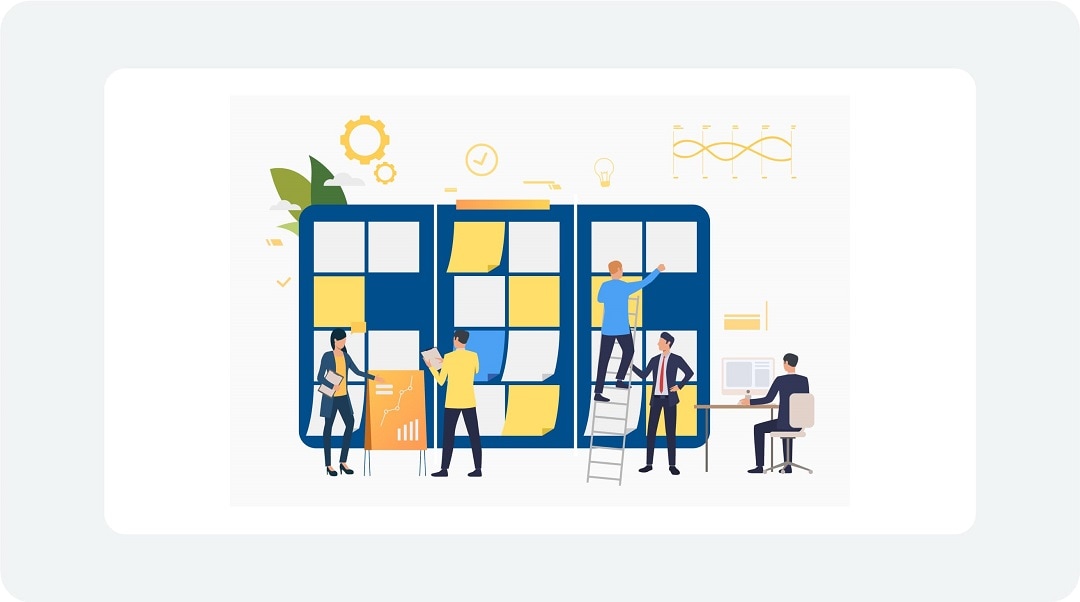
Part 2: History of Kanban
The Kanban system was developed in the mid-20th century by Toyota engineer Taichii Onho. It originated at Toyota Motor Corporation, a Japanese car manufacturer. The term “Kanban” combines two Japanese words: Kàn (sign) and Bǎn (board), reflecting the essence of the method.
In the 1940s, Toyota sought to increase productivity and reduce unnecessary material usage. Taichi Ohno introduced Kanban cards for workers to request more parts, minimizing excess inventory.
This approach eventually evolved into Toyota’s just-in-time (JIT) inventory system, inspired by American supermarkets where stock is replenished based on demand rather than periodic restocking.
This innovation transformed manufacturing, shifting from a push system (producing based on forecasts) to a pull system (producing based on demand). Initially implemented at Toyota, the system proved efficient, responsive, and waste-free, influencing the automotive industry and beyond.
Into the IT Industry
In the early 2000s, David J. Anderson adapted Kanban for IT and software development, emphasizing visualizing workflows, limiting WIP, and enhancing efficiency. Today, Kanban is widely used across industries for its simplicity, adaptability, and ability to boost productivity.
Part 3: Purpose of Kaban
Kanban aims to simplify work processes by making them easy to visualize and share, enabling more effective management.
Tools like the Kanban board transform workflows into visual processes, helping identify bottlenecks and apply existing knowledge to improve efficiency.
A primary goal of Kanban is to prevent workflow over-processing. By limiting work in progress (WIP), teams can focus on fewer tasks simultaneously, enhancing efficiency and reducing lead times. This systematic approach minimizes bottlenecks, accelerates workflow, and ensures smoother task completion.
Kanban also emphasizes continuous improvement. By monitoring and analyzing workflows periodically, teams can make incremental changes that refine processes over time.
Additionally, the visual nature of Kanban fosters better communication and collaboration, offering a clear overview of tasks and enabling teams to brainstorm solutions together. This results in better decisions, increased accountability, and improved outcomes.
Part 4: Types of Kanban Systems
Kanban systems have evolved from simple workflow management systems to six different types to meet the needs of industries.
Production Kanban
In manufacturing, it is used to trigger the start of production or reorder of stock; products are only manufactured according to the demand as a way of preventing over-production.
Withdrawal Kanban
This type is used to show the transfer of materials and products from one step to another, which is essential in managing the movement of products within a firm or between different firms in a supply chain.
Supplier Kanban
This type of Kanban is an expanded one. It goes beyond the company's internal supply chain. It helps include external suppliers in the lean inventory delivery management process. Its goal is to deliver the materials needed for production.
Emergency Kanban
Emergency Kanban is intended to be used only in extraordinary circumstances where there is an immediate need for the material or a deficiency has been identified, helping to establish priorities.
Throughput Kanban
Mainly concerned with the throughput of work in a system, this type is frequently found in service-centered businesses to improve the functioning of processes.
Express Kanban
To address the high-priority issues, Express Kanban allows for prioritized work on the items that are important and need to be completed rather quickly, but this is done without interfering with the general process.
Such Kanban systems enable organizations to optimize the processes, response time, and productivity to their preferences.
Part 5: Pros and Cons of Kanban
Pros
- Kanban gives a visual view of work. Teams can use it to track tasks, find bottlenecks, and monitor progress in real-time.
- Kanban can be easily implemented in many industries and teams, meaning changes to the current process do not need radical alterations to the Kanban system.
- Estimating work in progress (WIP) helps teams. It makes them focus on finishing work. It reduces overlap and improves workflow. It assists in establishing efficient procedures and eliminates time-consuming loops.
- Kanban provides for the constant review of the system and small enhancements. You can check the workflow often. Then, we can make small changes to improve the team's performance based on limited data.
- Kanban is a visual tool. It makes work transparent. It promotes consumer needs by involving the team in the process. It is transparent for everyone to see the workflow, thus making it easier to collaborate and address problems.
- Kanban focuses on product demand. It helps cut stock and limit overproduction, which is important in manufacturing.
Cons
- Kanban does not possess deadlines or time bounds by default. With due dates for the assignments, teams may be able to meet deadlines for time-bound projects.
- Kanban is more applicable and relevant to work in the short term and might not be very beneficial for planning and estimating in the long term.
- using Kanban to coordinate related tasks can be tough in complex or large projects. It can also mean incorporating other project management methodologies into the mix.
- Working well in a Kanban method requires teams to update the board and maintain the right work limit. However, with structure and order, it can become manageable and effective.
- Kanban is best for a dynamic process. It adds rigidity to those with a strict, efficient workflow.
Part 6: Kanban Examples
Here are several Kanban board examples for specific tasks. They prove that this method improves efficiency and structure in work processes.
Software Development Kanban Board
This board is used primarily by software development teams to track the project status. Projects consist of tasks represented by cards in the turnpike that pass through phases such as “Backlog,” “In Development,” “Testing,” and “Done. ”
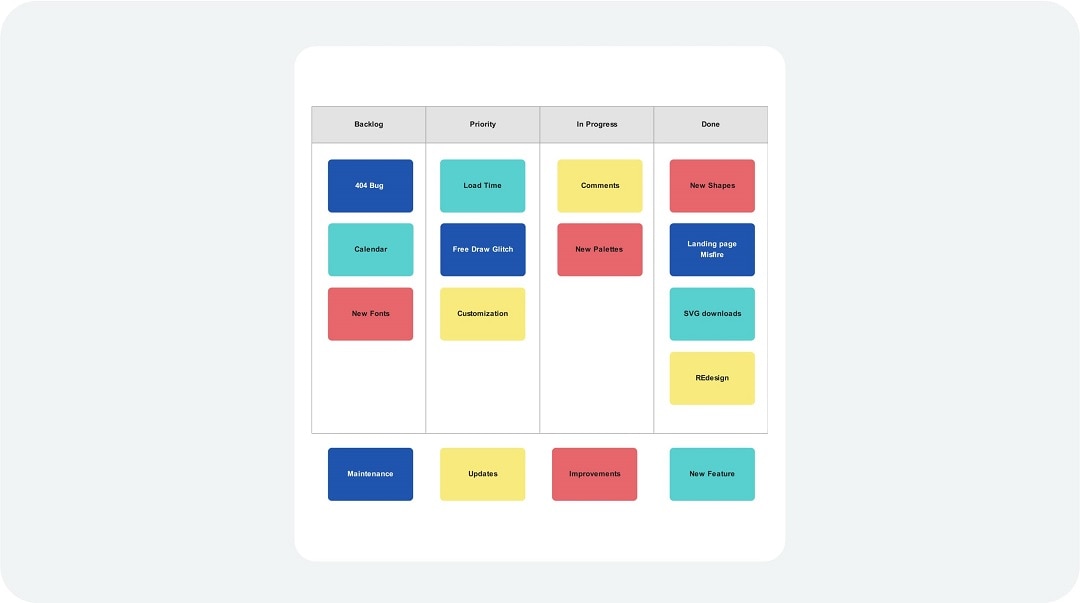
Marketing Kanban Board
A marketing team can utilize it as a marketing campaign management board. Some activities include writing the content, posting it at the right time, and reviewing performance. This process goes through 'to do,' 'in process,' and 'done.'
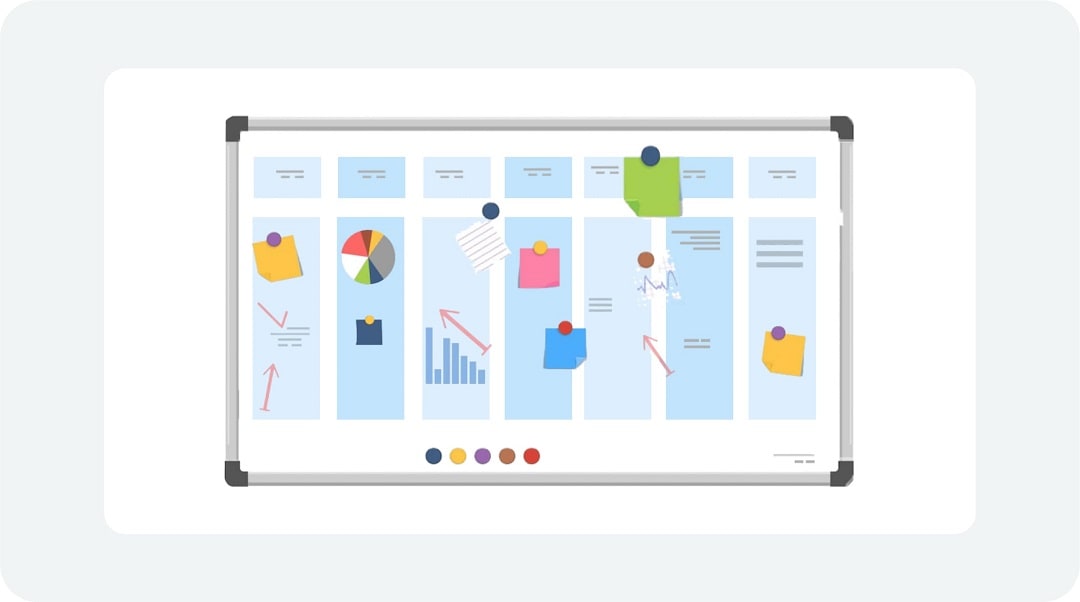
Customer Support Kanban Board
Customer support teams use this board to address customer concerns. For instance, email replies and ticket solving have statuses like "New", "In Progress", and "Resolved".
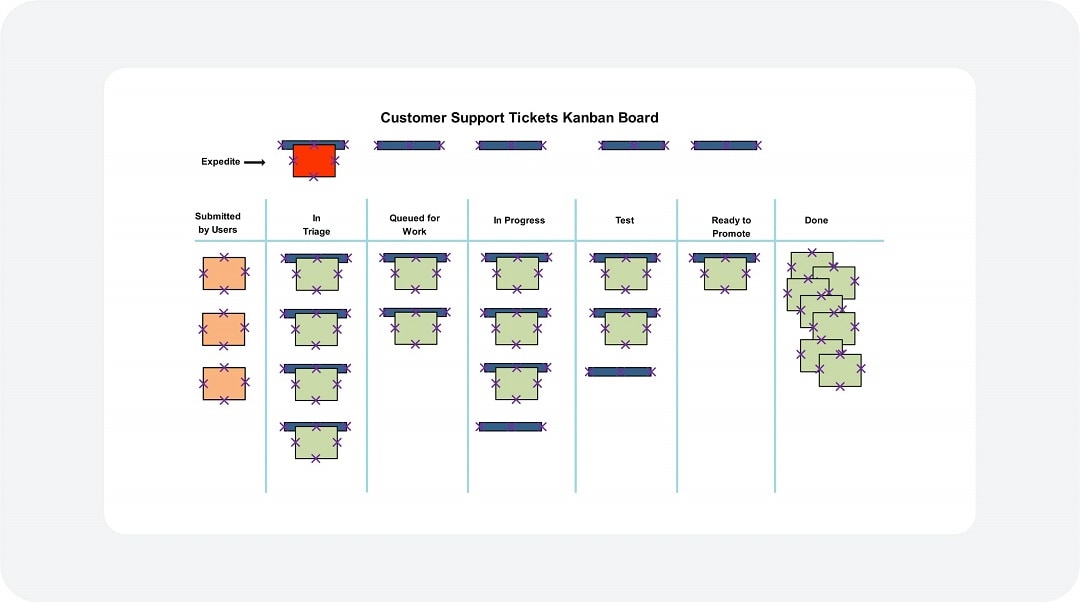
Project Management Kanban Board
It helps project managers monitor tasks in their projects. They include the planning, implementation, and control phases. They ensure timely and efficient delivery.
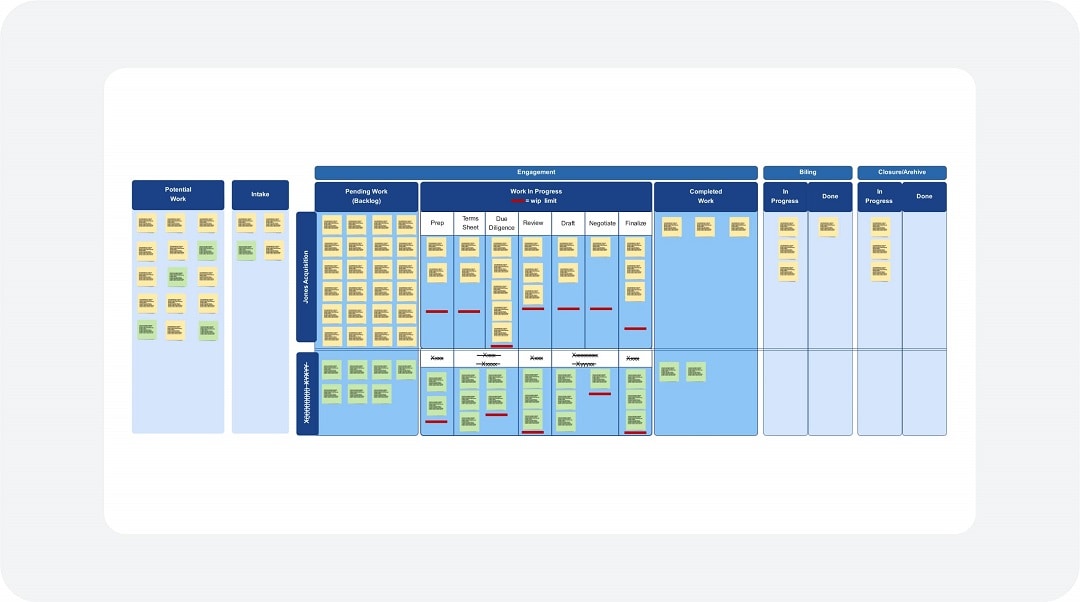
Personal Kanban Board
You can use the Personal Kanban Board as a list of individual responsibilities. Use this board for a list of tasks, like errands and chores. It tracks work through the steps: To Do, Doing, and Done.
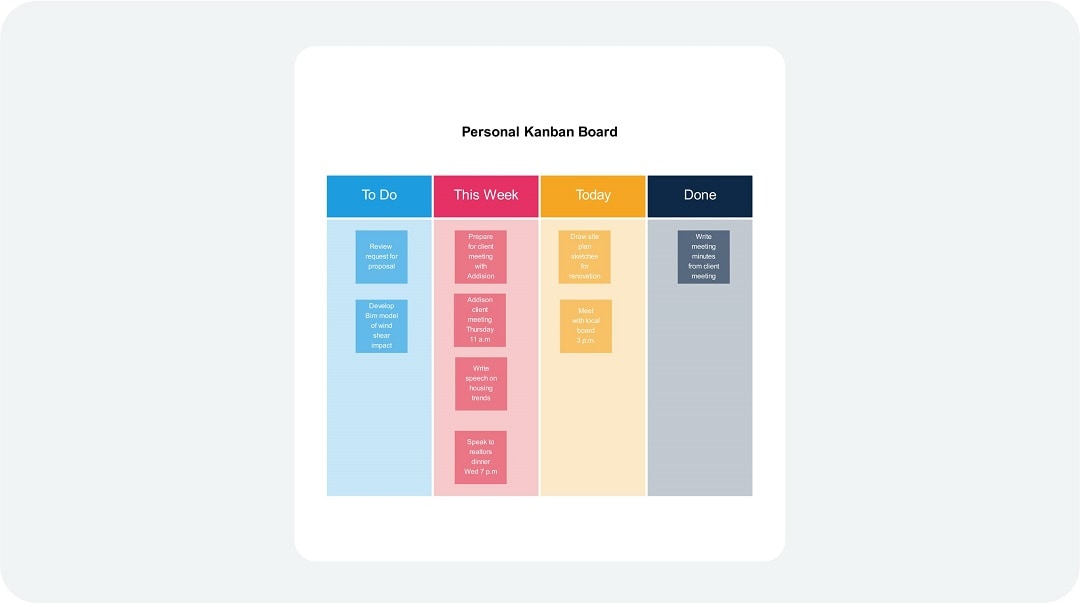
Part 7: What Are Kanban Boards
Kanban boards are among the simplest and most widely used tools for managing tasks and projects. Originating from the Kanban process developed for production lines, these boards have become essential across various industries.
A standard Kanban board features three columns: “To Do,” “In Progress,” and “Done.” Tasks are represented as cards or sticky notes, placed in the appropriate column based on their status. As tasks progress, they are moved from one column to the next, providing a clear, time-saving way to track workflow.
The benefits of Kanban boards are numerous. They enhance efficiency, promote collaboration, and drive continuous improvement. By limiting the number of tasks in the same stage, Kanban boards help teams focus and prevent inefficiencies.
They also foster teamwork by offering visibility into each member's progress and allowing quick identification of bottlenecks to target improvements, ensuring smoother workflows and better results.
Part 8: What Are Kanban Cards
Kanban cards are essential elements of the Kanban framework, forming the core of the visual system used to manage work. Each card represents a specific task or activity, providing a clear and concise project overview.
Typically, Kanban cards include task descriptions, due dates, assignees, and attachments. As tasks progress, the cards move across the Kanban board, enabling teams to monitor workflow, identify bottlenecks, and address issues in real time.
Beyond simplifying task management, Kanban cards enhance team collaboration and workflow. They help organize tasks, streamline processes, and ensure successful project completion by visually highlighting work in progress.
Part 9: How to Create a Kanban
Step 1: Choose the Right Tool
Select a platform for your Kanban board, such as a physical whiteboard or a digital tool like EdrawMind. Base your choice on your team’s preferences and required features.

Step 2: Create Workflow Columns
Set up columns on the board to represent different workflow stages. These columns help organize tasks and make it easy to track progress visually.
Step 3: Add Task Cards
Create individual cards for each task, including key details such as descriptions, due dates, assignees, and priorities. These cards are the building blocks of the Kanban board.
Step 4: Update Task Status
Move task cards across columns based on their current status. This visual flow lets you monitor progress and quickly identify bottlenecks or delays.
Step 5: Regularly Review the Board
Periodically review your board to ensure it remains functional and effective. Adjust columns, stages, or prioritization processes as needed to fit evolving team goals.
Step 6: Set WIP Limits
Establish Work in Progress (WIP) caps for each column to limit the number of ongoing tasks. This helps maintain focus and prevents overloading team members.
Step 7: Track Performance
Monitor key performance indicators to identify areas for improvement and encourage continuous workflow optimization.
Conclusion
Kanban systems are highly effective tools for improving workflow across various industries. With six types of Kanban—Production, Withdrawal, Supplier, Emergency, Throughput, and Express—you can tailor the system to meet specific needs, whether in manufacturing, software development, or personal tasks.
Using visuals and graphics keeps the team informed about each member's progress and activities, enhancing communication and transparency. This makes the system both flexible and efficient. While Kanban is particularly suited for simple, short-term projects, it offers significant benefits in time management and efficiency. Kanban can greatly enhance organization and deliver excellent results when properly adapted to the workflow and regularly updated.
