My years in manufacturing have shown me how quickly production can go off track. Miscommunication, overstocked inventory, and sudden slowdowns are all too familiar.
Kanban, a visual system, can help you fix that. It shows you what, when, and how much to produce.
In this write-up, I’ll explain its main principles, benefits, and uses in manufacturing. Plus, I’ll add tips from my experience to help you apply Kanban effectively.
So whether you’re experienced or just starting, these insights will be helpful for your operations.
In this article
Part 1: What Is Kanban?
Born from Toyota’s approach to manufacturing, Kanban uses cards to keep track of tasks, making it easy to see where things stand.
Main Principles of A Kanban
Kanban revolves around four fundamental principles:
- Visualize the workflow: Make a board with columns for each stage—To Do, In Progress, and Done. Each task gets a card, moving from stage to stage as it’s worked on.
- Limit Work-in-Progress: Only work on a few tasks simultaneously, keeping focus and preventing overload. Once a task is done, you start a new one, keeping the process moving.
- manage the flow: The visual setup helps teams see problems early so that they can adjust. Regularly reviewing the board with others helps find ways to improve and stay on track.
- Supports constant growth: Teams routinely look for ways to improve, aiming to reduce waste and enhance efficiency. This ongoing improvement keeps work responsive to changing needs.
Part 2: Examples of Kanban in the Manufacturing Industry
Inventory Control
The bullwhip effect can cause havoc—little shifts in customer demand can create huge ripples through your supply chain. Kanban helps steady your inventory management.
Each item is linked to a Kanban card, forming a feedback loop. The card signals an immediate restock when an item hits its reorder point.
For instance, a Kanban card on a resistor reel in a PCB line notifies the staff to restock as it nears empty. It ensures the line keeps moving.
Production Scheduling
The Kanban board is a roadmap for your production line. Each column represents a step in your workflow, and each card marks a task.
This setup lets your crew see the big picture with a glance. If a bottleneck forms, it’s obvious to let you make adjustments immediately.
Quality Control and Lean Manufacturing
Visualizing the flow lets you add quality checks at each stage. Spotting defects ahead of time minimizes rework and keeps standards high. Focus on limiting WIP reduces waste and builds a lean, streamlined manufacturing process.
For example, in a furniture workshop, a Kanban card for a chair frame might list quality checks, starting with wood cutting and finishing with the final stage.
Communication and Coordination
With a Kanban board, checking task status is easy and quick, no matter who’s looking. The board offers a quick overview so every team member avoids time-consuming check-ins. Suppliers get transparent details on what’s required and when.
Employee Task Management
Limiting work-in-progress keeps employees from juggling multiple tasks, which reduces errors. With only one task to focus on at a time, employees work more efficiently and feel less strain.
Part 3: Benefits of Using Kanban in Manufacturing
Kanban does more than map your workflow—it optimizes everything. Here’s how:
Just-in-Time Production: Only manufacture what’s necessary and exactly on time. This reduces waste and enhances efficiency. We lowered our raw material storage costs by 12% after adopting Kanban.
Enhanced Process Visibility: Kanban gives a live view of your production, letting you spot issues quickly. Our team once detected a slowdown at assembly due to a faulty machine, avoiding a critical delay.
Balanced Workload: Work-in-Progress (WIP) limits prevent task overload, keeping the workflow steady. We’ve witnessed project completion times drop by 20% by setting task caps.
Quality at Every Step: Kanban includes quality checks at each stage, helping catch defects early and minimizing rework. Our defect rate dropped by 10% with Kanban and visual checks in place.
Better Team Coordination: Kanban clarifies tasks and responsibilities, boosting accountability and collaboration. In my experience, this system has enhanced communication, leading to a more engaged, productive environment.
Part 4: Tips for Using Kanban in Manufacturing
Kanban can streamline manufacturing workflows when used effectively.
Set WIP Limits: Don’t overwhelm your team—restrict tasks at each stage to a manageable level, like 3-5. This helps maintain steady progress without overloading anyone.
Color to Prioritize: Use colors on the Kanban board to make priorities visible. For instance, you can use red for urgent, yellow for regular, and green for flexible tasks to inform everyone exactly where to focus.
Get the Team Involved: Kanban shines with collaboration. Host short meetings daily to discuss the board, welcome feedback, and brainstorm solutions for potential holdups. This keeps everyone engaged in improving the workflow.
Monitor Key Metrics: Tracking data like lead time and cycle time gives you a clear picture of performance. Use this information to continually enhance the workflow.
Adapt as You Go: Kanban is dynamic. Adjust your board setup as production demands shift or the team needs to evolve. Plus, regular reviews keep your Kanban effective.
Part 5: How to Create a Kankan for Manufacturing
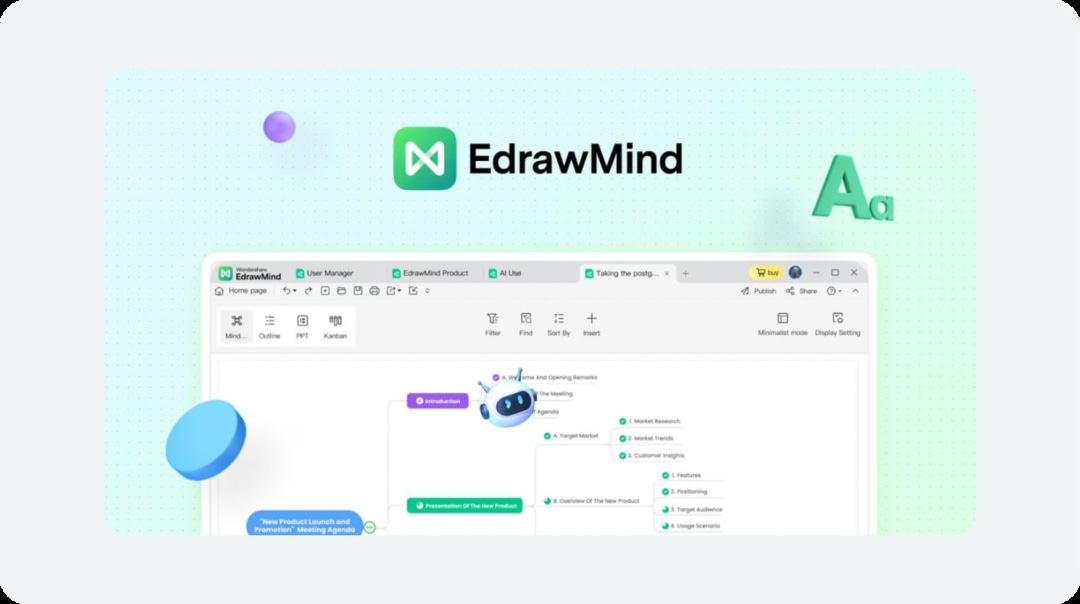
Running a Kanban process well requires a solid platform. Sticky notes and whiteboards are outdated when it comes to managing workflows. EdrawMind is an advanced, practical option for putting Kanban principles into action.
It makes applying Kanban principles easy and efficient. You can build boards that clearly show tasks, priorities, and progress. The user-friendly interface makes organizing workflows, assigning roles, and collaborating simple.
Though it requires a purchase, its real strength is simplifying complex Kanban workflows.

How to Create Your Kanban in EdrawMind?
Step 1 Start a New Mind Map
Open the EdrawMind desktop app and create a new mind map. Click New Mindmap for a fresh start.
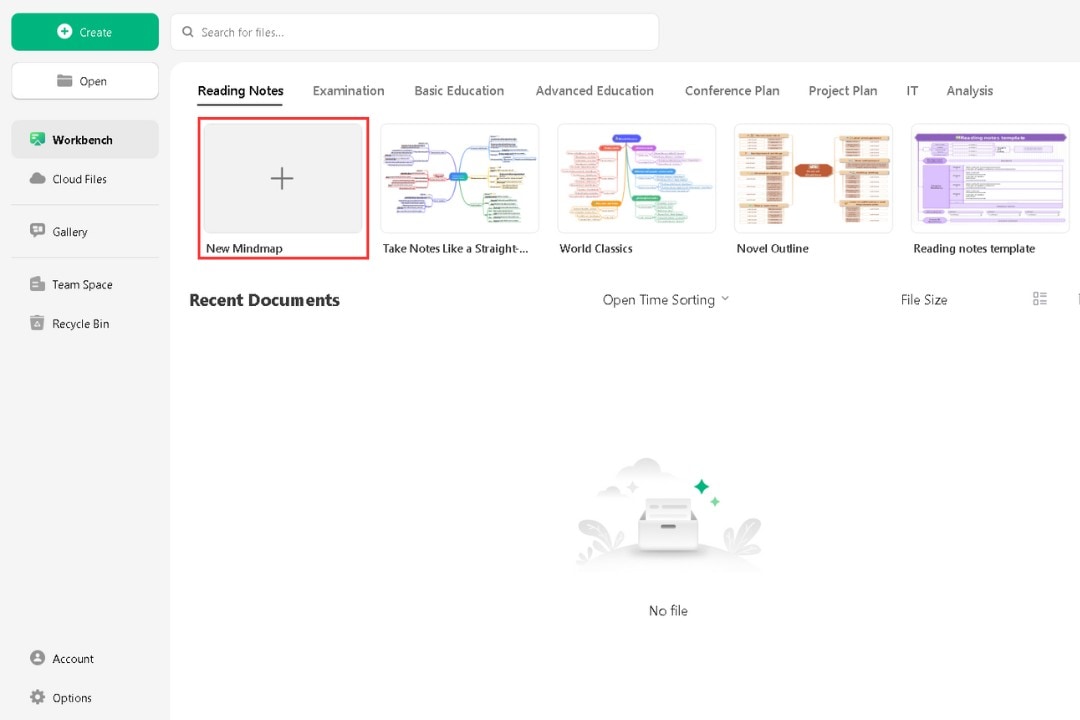
Step 2 Set Up Workflow Columns and Customize Layout
Locate the Kanban button in the toolbar and click it to switch to the Kanban view.
Set up your columns to represent your workflow steps, like To Do, In Progress, and Done.
Use the + Add Group icon to add any other columns you need for your project. You can also personalize your Kanban board. Change card colors, add icons, or attach files from the right-side menu for clear context.
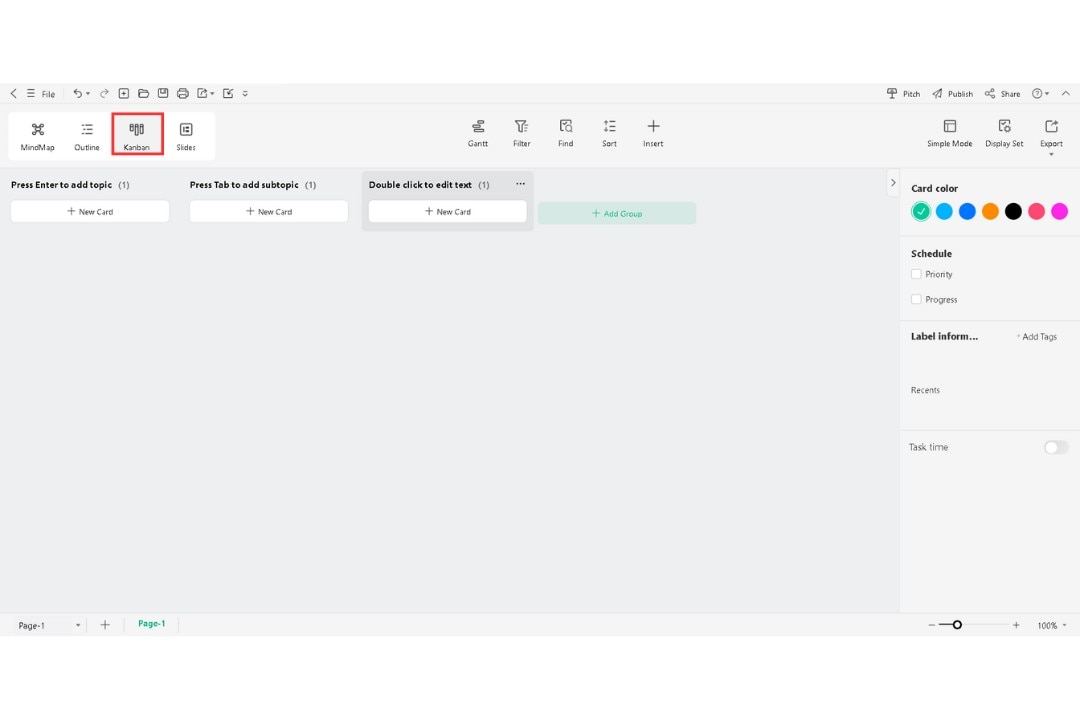
Step 3 Add Tasks and Details
Add tasks to each column. Use the New Card button to create cards for your tasks.
Double-click on any text box to add details like the task name, description, and due date if required.
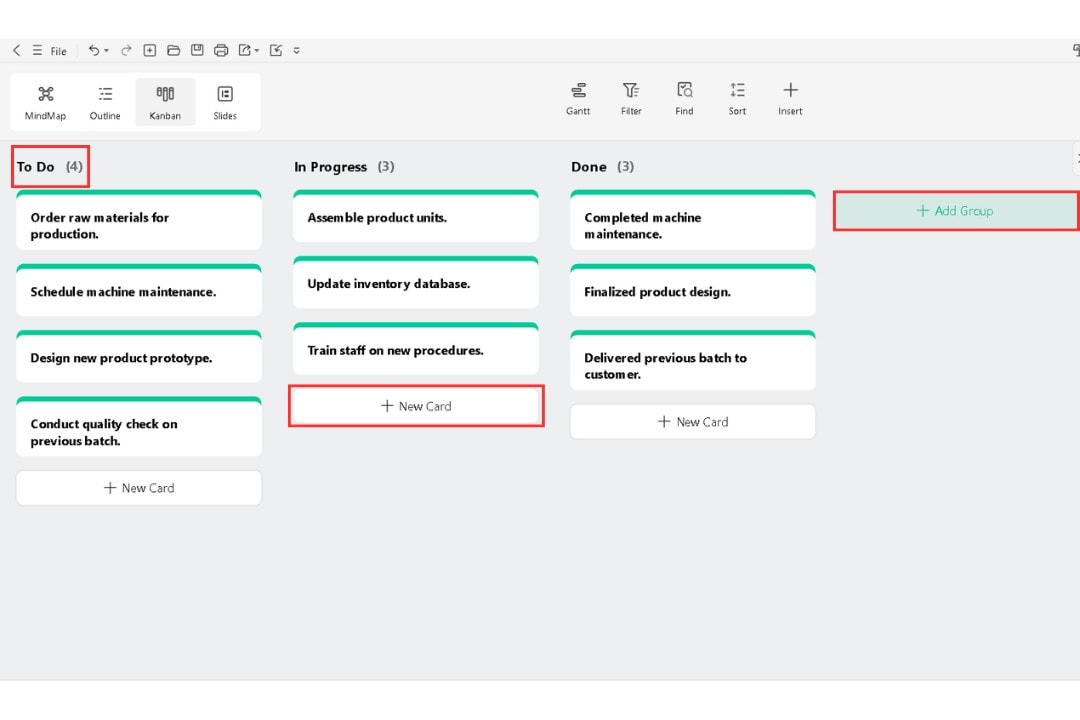
Step 4 Export Your Board
After setting up your board, save it by clicking the Export button. Then, select More Formats, adjust the settings, and download it to your device.
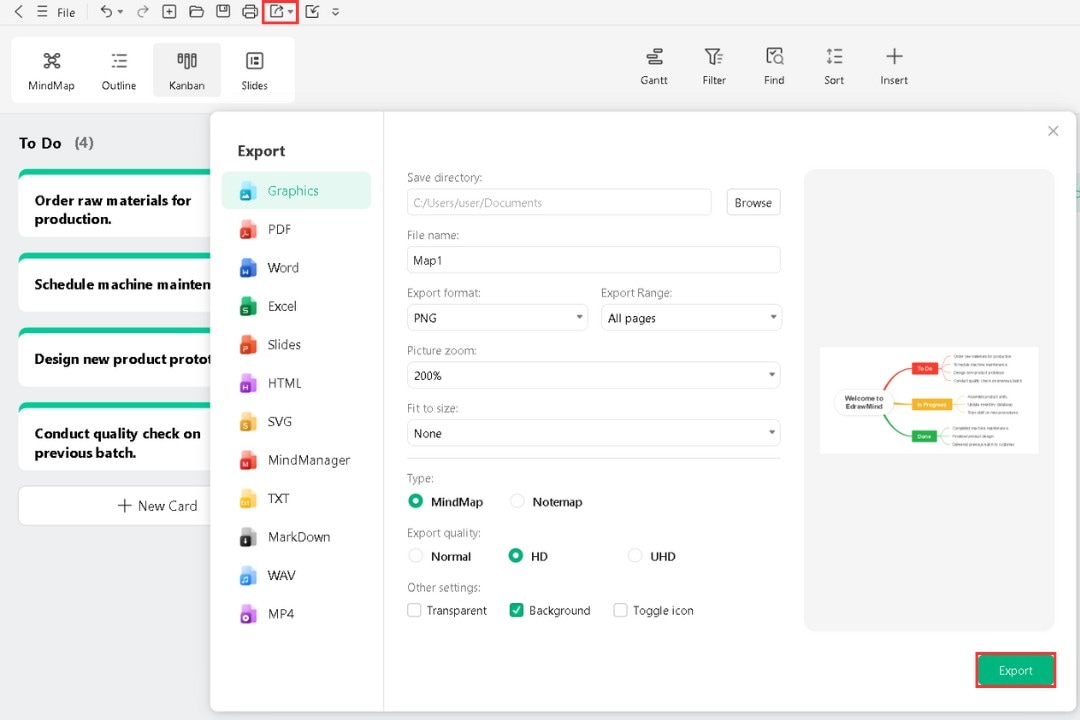
Part 6: Common Pitfalls to Avoid
Kanban can indeed improve your production process, but some traps can slow you down. I’ve seen these issues firsthand on the production floor, so here’s what to avoid.
Too Many Columns: Adding columns and flags can seem helpful but can often add confusion. I’ve seen teams overwhelmed by boards with too many sections. Focus on the essentials like To Do, In Progress, and Done for clarity.
Neglecting Metrics: Moving tasks alone won’t reveal the whole story; metrics are crucial. Cycle time (task duration) and lead time (from delivery request) give valuable insights. Tracking cycle time once helped us notice delays in quality checks, cutting our production time by 10%.
Refusing to Adjust: Kanban boards need updates as your workflow evolves. I’ve adjusted columns, WIP limits, and steps to meet changing demands.
Unclear Labels and Colors: Kanban thrives on clear visuals. Use short labels and a simple color code, like red for urgent, yellow for attention, and green for standard. This clarity keeps your crew aligned.
Too-Tight WIP Limits: While WIP limits keep things balanced, setting them too low can slow you down. I saw this firsthand; easing limits slightly kept things moving smoothly.
Conclusion
Kanban makes work, production, and collaboration better. In my experience, Kanban works best when you mold it to your production setting.
Tools like EdrawMind can help lay out your processes, track each phase, and gradually improve.
So, If you're ready to take a step forward, EdrawMind can help create a transparent, more productive workspace.
